Hey guys. Long time no speak.
I've been working on a project which involves converting a stock log intake into a triple carby manifold. As you can see in the photos Ive simply welded on 2 additional carb mounts between the runners for 1 and 2 as well as 5 and 6. The plenum is completely open. No segregation.
Here you can see it fitted with 3 single barrel Stromberg carbs (1 1/32 venturi) which flow about 162cfm at 3"Hg or if converted to compare to 4-barrel carbs, which are measured at 1.5"Hg 1 1/32" = 114cfm. Either way it provides a total of over 340 cfm. I havent run this set up yet.
Now to the purpose of this post.
My actual question......If I decide to go down the turbo route, could I effectively use this manifold with a single carby (ie 600 holley) draw through turbo and have the pressurised air from the turbo split into the 3 ports? Effectively creating a new "plenum" which collects the pressurised air/fuel and then feeds the 3 intake ports.
Would it work much worse than using my Offy intake?
For now I'd rather not debate the pro's/cons of draw thru versus blow thru.
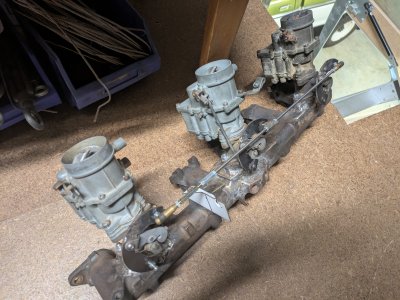
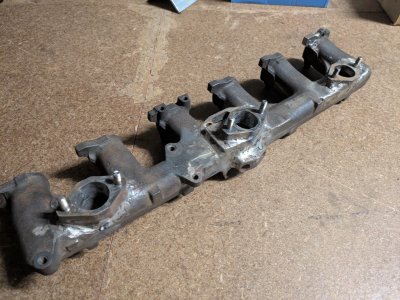
I've been working on a project which involves converting a stock log intake into a triple carby manifold. As you can see in the photos Ive simply welded on 2 additional carb mounts between the runners for 1 and 2 as well as 5 and 6. The plenum is completely open. No segregation.
Here you can see it fitted with 3 single barrel Stromberg carbs (1 1/32 venturi) which flow about 162cfm at 3"Hg or if converted to compare to 4-barrel carbs, which are measured at 1.5"Hg 1 1/32" = 114cfm. Either way it provides a total of over 340 cfm. I havent run this set up yet.
Now to the purpose of this post.
My actual question......If I decide to go down the turbo route, could I effectively use this manifold with a single carby (ie 600 holley) draw through turbo and have the pressurised air from the turbo split into the 3 ports? Effectively creating a new "plenum" which collects the pressurised air/fuel and then feeds the 3 intake ports.
Would it work much worse than using my Offy intake?
For now I'd rather not debate the pro's/cons of draw thru versus blow thru.
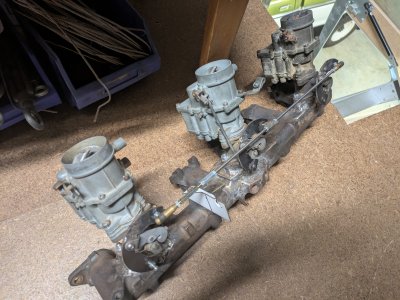
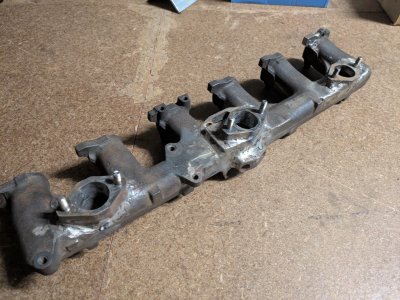