Tonight I finished polishing the 5 remaining combustion chambers with the 120 grit buffing pad. Then I went back to the first one and hit it with the 180 grit pad. I can’t really tell a difference so I’m not sure I’m going to do the rest. In the pic below, the one on the right is the 180 and the one on the left is 120.
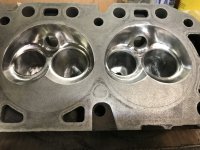
I still need to work in the exhaust ports some more.
In unrelated news, I was thinking about shift point a little more and remembered the first gen Lightnings. I did some research and confirmed that they had a 5000rpm shift point. So by getting on of those ECMs I should be able to have a 5000rpm shift point instead of 4500. I’m not sure if it’s appropriate for this build or not, but at least it’s something I can consider.... especially since I’m still in the planning phase. Is it worth it? Will it make a large difference? I’m not sure yet. Any thoughts anyone?
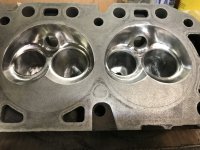
I still need to work in the exhaust ports some more.
In unrelated news, I was thinking about shift point a little more and remembered the first gen Lightnings. I did some research and confirmed that they had a 5000rpm shift point. So by getting on of those ECMs I should be able to have a 5000rpm shift point instead of 4500. I’m not sure if it’s appropriate for this build or not, but at least it’s something I can consider.... especially since I’m still in the planning phase. Is it worth it? Will it make a large difference? I’m not sure yet. Any thoughts anyone?