One of the first things you often hear is about picking a turbocharger that will spool.
That is not the objective.
The main goal is to pick a turbocharger that is the correct size for the engine and its application.
An engine is an air pump that has a range of airflow from the beginning of its power band to the end of its power band.
The turbocharger's compressor is likewise an air pump that has a flow range from the surge line out to the choke line.
Most of the 300 sixes discussed on this forum are for street use in a truck that works best with a wide power band.
In order to achieve the widest power band with a turbocharger, the flow range of the turbocharger should be matched with the flow range of the engine.
Drag racing is an entirely different story.
The following calculator is the best there is and will be used for the rest of this discussion.
www.borgwarner.com
That is not the objective.
The main goal is to pick a turbocharger that is the correct size for the engine and its application.
An engine is an air pump that has a range of airflow from the beginning of its power band to the end of its power band.
The turbocharger's compressor is likewise an air pump that has a flow range from the surge line out to the choke line.
Most of the 300 sixes discussed on this forum are for street use in a truck that works best with a wide power band.
In order to achieve the widest power band with a turbocharger, the flow range of the turbocharger should be matched with the flow range of the engine.
Drag racing is an entirely different story.
The following calculator is the best there is and will be used for the rest of this discussion.
BorgWarner MatchBot
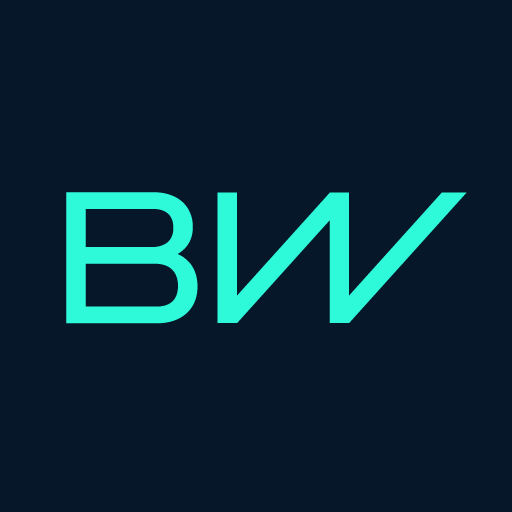
Last edited: