Hello all,
Iv been enjoying this site along with the turbo sixes facebook group for a while now. I finally have made some progress on my build so I wanted to share so others can see and pass along advice where my knowledge is lacking.
I have a 1966 F100 short bed (yes the front end is from a ‘64 I know) that I picked up a few years ago. Got the truck back on the road and I have been modifying and fixing as I go. Iv put around 5k on the truck and its been great so its time to mess that up by going with a turbo on the truck! As of now the truck has a crown vic front suspension and a crown vic rear axle. The rear end has been C notched, running leaf springs with a watts link. What I believe to be the original 300ci is under the hood because the vin shows it was a factory straight six truck and the casting date on the block matches up. Behind the 300 I put a T5 5 speed and it has made the truck a dream to drive. The truck will cruse at 75mph and on the 5 hour drive to the the F100 show a month back it was getting 18mpg.
Here is how the truck started out vs. how it looks today
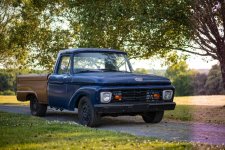
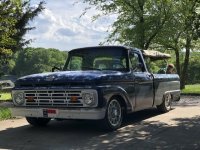
The plan has always been to turbo the 300 in the truck but I wanted a solid starting point. So the last 3 years has been getting it back on the road and modified to make it a fun driver with modern day traffic.
The first step to turbocharging the truck was to get a mock up motor. Something I could build the turbo kit with, without taking the truck off the road. So I sourced a rebuilt 70’s motor with 30 over pistons and brought it home. The other plan for this motor is to have a spare incase the motor in the truck looses oil pressure or something like that. I don’t want to take it of the road any longer then I have to!
Once I finish the turbo kit I plan to build the mock up motor for boost with some added ring gap, ARP hardware, and forged pistons if I can find a good set to fit it.
Im not going over the top with this turbo build the plan is not for max power but really the sound and cool factor. Plan is to run 6-8psi and turn it up to 12psi to play from time to time. My T5 won’t handle much so I will keep skinny tires as a way to save some stress on the trans.
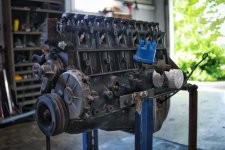
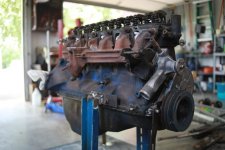
Iv been enjoying this site along with the turbo sixes facebook group for a while now. I finally have made some progress on my build so I wanted to share so others can see and pass along advice where my knowledge is lacking.
I have a 1966 F100 short bed (yes the front end is from a ‘64 I know) that I picked up a few years ago. Got the truck back on the road and I have been modifying and fixing as I go. Iv put around 5k on the truck and its been great so its time to mess that up by going with a turbo on the truck! As of now the truck has a crown vic front suspension and a crown vic rear axle. The rear end has been C notched, running leaf springs with a watts link. What I believe to be the original 300ci is under the hood because the vin shows it was a factory straight six truck and the casting date on the block matches up. Behind the 300 I put a T5 5 speed and it has made the truck a dream to drive. The truck will cruse at 75mph and on the 5 hour drive to the the F100 show a month back it was getting 18mpg.
Here is how the truck started out vs. how it looks today
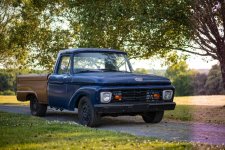
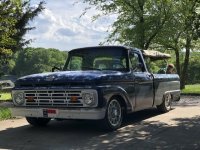
The plan has always been to turbo the 300 in the truck but I wanted a solid starting point. So the last 3 years has been getting it back on the road and modified to make it a fun driver with modern day traffic.
The first step to turbocharging the truck was to get a mock up motor. Something I could build the turbo kit with, without taking the truck off the road. So I sourced a rebuilt 70’s motor with 30 over pistons and brought it home. The other plan for this motor is to have a spare incase the motor in the truck looses oil pressure or something like that. I don’t want to take it of the road any longer then I have to!
Once I finish the turbo kit I plan to build the mock up motor for boost with some added ring gap, ARP hardware, and forged pistons if I can find a good set to fit it.
Im not going over the top with this turbo build the plan is not for max power but really the sound and cool factor. Plan is to run 6-8psi and turn it up to 12psi to play from time to time. My T5 won’t handle much so I will keep skinny tires as a way to save some stress on the trans.
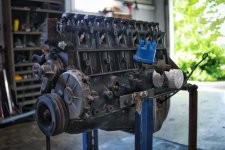
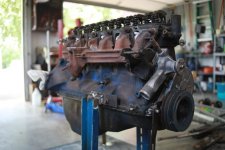