Thanks, Wesman. It's my sincere hope this information helps people fix these vehicles and keep them on the road.
Another sure sign you have an EEC-IV is the presence of an E core ignition coil instead of a Duraspark barrel coil. E core coils are named for the layers of ferrous plates shaped like an 'E' and stacked together with wire coiled through the legs. E core coils are generally reliable, and since '86 I've only replaced a handful. The connection to key power and module is unsealed and can cause issues, but the connector pigtail is available and the terminals can be cleaned in the event of misfires. A little dielectric goes a long way.
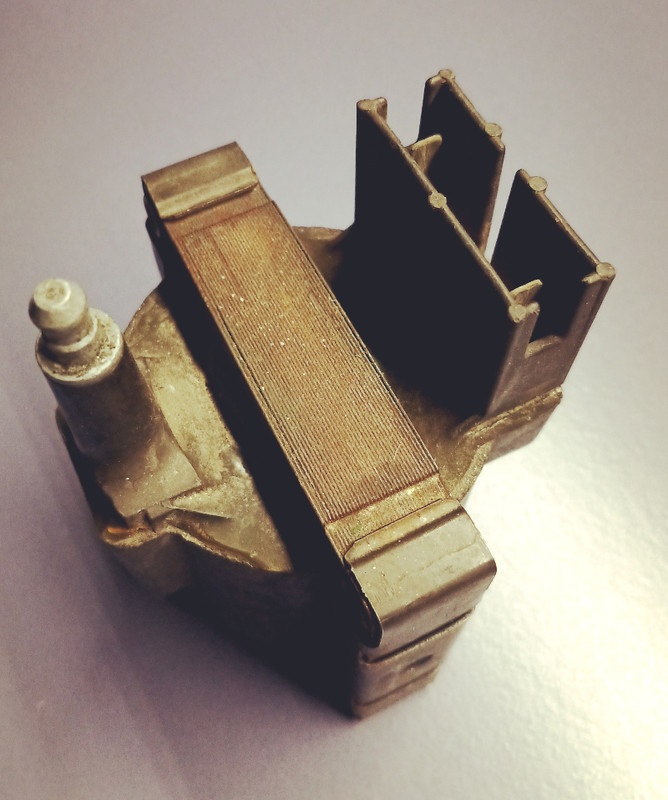
I should briefly talk about TFI issues. As we all know, heat is the nemeses of TFI modules. As I mentioned earlier, I carry a spare module, just as I carried a backup ballast resistor in all the vintage Chryslers I've owned. It's the reason Ford moved them to heat sinks (well, that and the class action lawsuit). I've had one die on me right in the middle of the Spaghetti Bowl (Las Vegas) on a very busy day in my Mustang and had to scramble to get the thing to the side of the road in one piece. However, that's the only time it has happened, and where I live 115 degrees F is normal. Many TFI problems can be eliminated by periodically removing the TFI, cleaning off the old dielectric and reapplying new.
I come from the age of bias ply tires, such on the road drama was normal back then, so that sort of thing typically doesn't freak me out.
Another sure sign you have an EEC-IV is the presence of an E core ignition coil instead of a Duraspark barrel coil. E core coils are named for the layers of ferrous plates shaped like an 'E' and stacked together with wire coiled through the legs. E core coils are generally reliable, and since '86 I've only replaced a handful. The connection to key power and module is unsealed and can cause issues, but the connector pigtail is available and the terminals can be cleaned in the event of misfires. A little dielectric goes a long way.
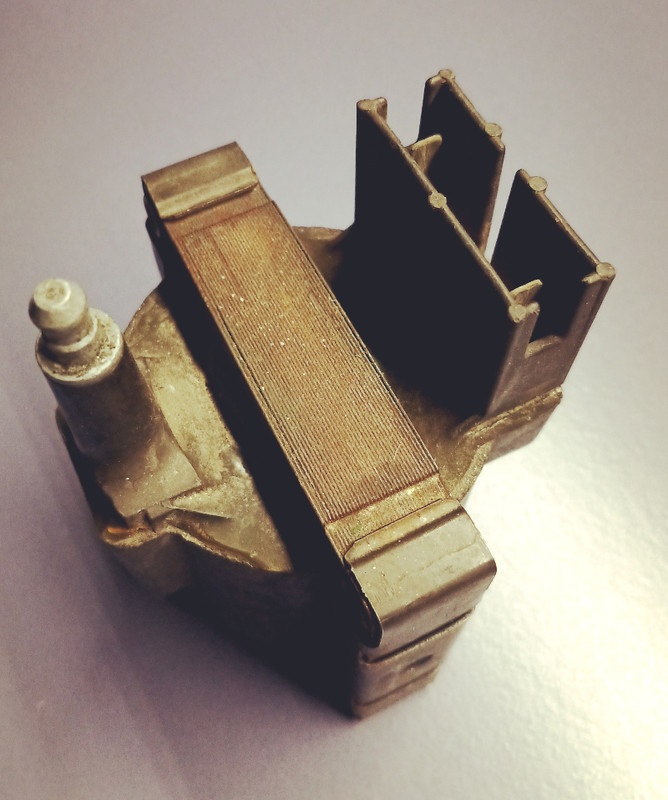
I should briefly talk about TFI issues. As we all know, heat is the nemeses of TFI modules. As I mentioned earlier, I carry a spare module, just as I carried a backup ballast resistor in all the vintage Chryslers I've owned. It's the reason Ford moved them to heat sinks (well, that and the class action lawsuit). I've had one die on me right in the middle of the Spaghetti Bowl (Las Vegas) on a very busy day in my Mustang and had to scramble to get the thing to the side of the road in one piece. However, that's the only time it has happened, and where I live 115 degrees F is normal. Many TFI problems can be eliminated by periodically removing the TFI, cleaning off the old dielectric and reapplying new.
I come from the age of bias ply tires, such on the road drama was normal back then, so that sort of thing typically doesn't freak me out.