Think of boost as a multiplier. The example of the stock 5.0 V8 also assumes you make it breathe like one, so the intakes on that example video flow about 130 CFM, and the exhausts 95 at mid-range .300 lift, the cam appropriate for the rpm, and so on. If you want to match those results, you have to reasonably match those parameters - with only 6 ports.

Multiply with a PR of 2 and you double your HP. PR 3 and triple it - actually a bit more as the parasitic losses are absorbed in that first NA PR, but we like conservative.
There are pros and cons to every path in forced-air. Most I work with go turbo, as they are (relatively) cheap, and much more configurable at lower cost, while the downside is some extra exhaust work to fit it in, along with the wastegate for most stuff over PR 2. Blowers are solid, more predictable as you don't have to figure how the exhaust will spin it up, but (relatively) expensive, with ducting, bracket and belt drive engineering. There's no single winner for everything.
What some call the 'turbo lag' is as much the increased power under the curve as it is "late" onset. So while it may feel lag, it also feels like you were missing more at first than you were as it exceeds boost and power compared to a supercharger's more-linear response, for a more "top hat" power curve. Power that follows throttle vs power that lags and exceeds throttle. It's different response and each fits different goals. While generic and assumptive, the following graph helps to explain this phenomenon:
Most superchargers are limited for boost level with pump gas, as the efficiency goes crappy pretty quick. Eaton for example cuts their M-charger maps at 2 PR, which is due to falling under 60% adn creating lots of heat, which is bad for both boost and detonation. I have a spare M112 here, and it would be a good fit for a 300, but only up to 2 PR (±15 psig) as you can see. A
stock 300 head at 76% VE would make 430 HP at 15 psi and ±510 M3/hr, and at the limit for this supercharger:
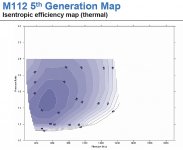
You can see it would take about 20% port flow improvements (with the other stuff) to hit 500 - but it's doable. So this is where you choose the fit to your project goals (yeah, that list), and accept the pros and cons for what fits your happiness.
