Ok people, ive been driving my lpg blown crossie for a while, but Ive only recently given it full throttle. When i did i got pinging when the manifold pressure approached 60 inches hg (15psi). Ive been running 25degrees BTDC fixed timing. So now it would appear that I need a pressure retard to stop this, I think 12 degrees retard would do it. So my idea is to fit a vacuum advance to my Bosch dizzy and connect this to the suction side of the supercharger. Then set the dizzy to 12btdc, the vacuum unit would pull this to 25 degrees at light loads and low manifold pressure but when vacuum gives way to boost this would drop back to 12, QED reducing pinging. Thoughts on this reasoning? I dont know of any electronic setup which could do this, other than the more comprehensive total control ECUs, which i dont want. See the piccie for reference.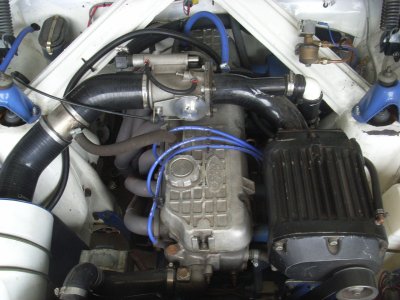
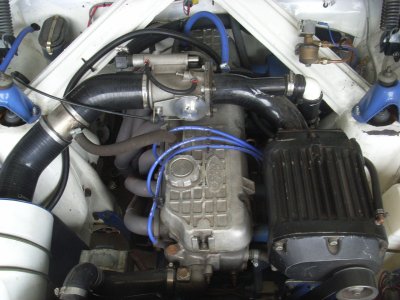
Last edited: