I've done a lot of research on roller cams in the past few months, to see if they can be installed in the US sixes. The answer is YES, but there were a few problems to overcome.
The first problem is roller core availability, since they are not produced. There are major differences in lobe profiles, thus making it impossible to grind a roller profile on a stock core. That being said, I've been working with the company that produces cores for Clay Smith Cams, and after a little prodding, they agreed to produce a roller core for FSPP. However, it should be noted that they will be more expensive due to the limited number required (standard run is 2000 cores). Problem one solved.
Installing roller lifters appears to be the other major problem, as they normally require tie bars. It would be difficult (at best) to install a pair of roller lifters into a US block with the tie bars inplace, but with a few modifications to the block, it is possible. However, we began looking at other possibilities and discovered that this is not necessary. We are working with Jesel and have come up with a design that eliminates the tie bars altogether. A special lifter is required, as well as machining the lifter bores, but it eliminates the use of tie bars. Problem two solved.
The last problem is the easiest to solve. There are no roller profiles established for inline six applications. Clay Smith Cams is currently developing new roller profiles, which will be suited to inline six applications. This will probably require new master profiles, which are expensive, so we will limit them to the most popular setups. However, we will be offering three or four profiles designed around the new aluminum head. Problem three solved.
Now, back to the lifters, as I'm sure you are wondering how we plan to eliminate the tie bars. Jesel already produces the required lifters; they just never intended them to be used in an inline six application. That's not surprising is it?
The lifters have a tiny knob that sticks out the side of the lifter. They are available in two styles, with a rounded end or a square end. To install them in the block you need to do one of two things. Machine a grove in the lifer bore which uses the round end, or re-machine the lifter bore (to a larger diameter) to accept a special brass lifter guide which uses the square end. The brass guides are manufactured with a groove that works with cams up to .500 lift (at the lobe), which is more than we would ever need. I'll see if I can get some pics of the lifters and guides posted.
The ones on their website have keyways as opposed to the peg style they showed us at PRI ??? Same concept. They are also very pricey at $175 per hole.
Guess you could use the keyway lifters on the one and six cylinders, and standard tie bar lifters on the other four to save a few bucks.
The first problem is roller core availability, since they are not produced. There are major differences in lobe profiles, thus making it impossible to grind a roller profile on a stock core. That being said, I've been working with the company that produces cores for Clay Smith Cams, and after a little prodding, they agreed to produce a roller core for FSPP. However, it should be noted that they will be more expensive due to the limited number required (standard run is 2000 cores). Problem one solved.
Installing roller lifters appears to be the other major problem, as they normally require tie bars. It would be difficult (at best) to install a pair of roller lifters into a US block with the tie bars inplace, but with a few modifications to the block, it is possible. However, we began looking at other possibilities and discovered that this is not necessary. We are working with Jesel and have come up with a design that eliminates the tie bars altogether. A special lifter is required, as well as machining the lifter bores, but it eliminates the use of tie bars. Problem two solved.
The last problem is the easiest to solve. There are no roller profiles established for inline six applications. Clay Smith Cams is currently developing new roller profiles, which will be suited to inline six applications. This will probably require new master profiles, which are expensive, so we will limit them to the most popular setups. However, we will be offering three or four profiles designed around the new aluminum head. Problem three solved.
Now, back to the lifters, as I'm sure you are wondering how we plan to eliminate the tie bars. Jesel already produces the required lifters; they just never intended them to be used in an inline six application. That's not surprising is it?

The lifters have a tiny knob that sticks out the side of the lifter. They are available in two styles, with a rounded end or a square end. To install them in the block you need to do one of two things. Machine a grove in the lifer bore which uses the round end, or re-machine the lifter bore (to a larger diameter) to accept a special brass lifter guide which uses the square end. The brass guides are manufactured with a groove that works with cams up to .500 lift (at the lobe), which is more than we would ever need. I'll see if I can get some pics of the lifters and guides posted.
The ones on their website have keyways as opposed to the peg style they showed us at PRI ??? Same concept. They are also very pricey at $175 per hole.


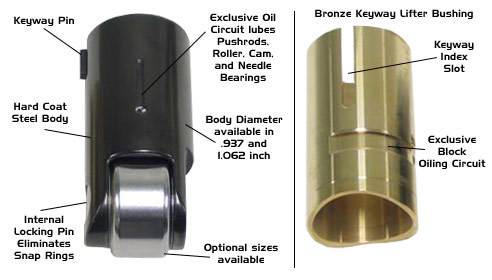