My original pathway needed to change after closely checking the carb base. I removed one of the brass plugs and it uncovered drilled passageways from the slots to the idle mixture screw. The original direction would have intercepted this passage and ruined the base. There was another route on the other side of the slot passage where I was drilling through solid material at a different elevation and would miss the passage.
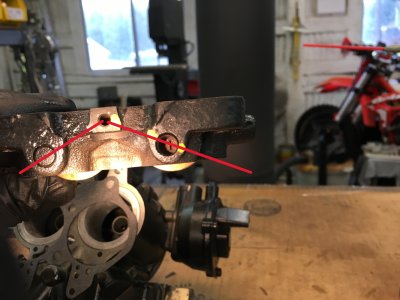
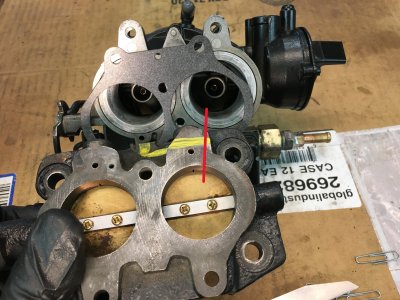
I cleared an area with a small burr and then used a spot facing bit to create a flat where I could measure carefully and mark where the hole was needed. This was the most stressful hole I think I’ve ever drilled.
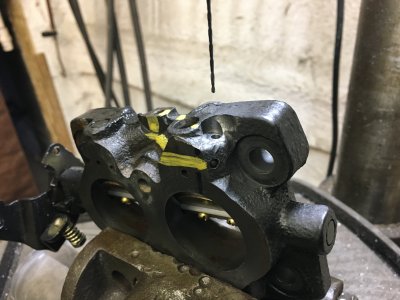
The hole came through the base just where I was hoping it would- just above the throttle blade. It felt a bit like operating a tunnel boring machine!
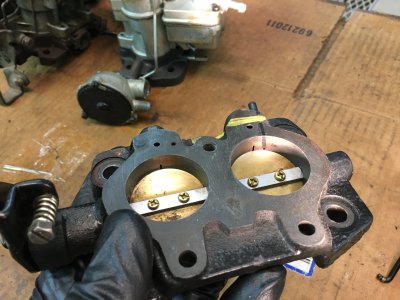
Placed a vacuum hose nipple into the outside of the hole with some epoxy; when that cures, I’ll reassemble and try it out. Fingers crossed!
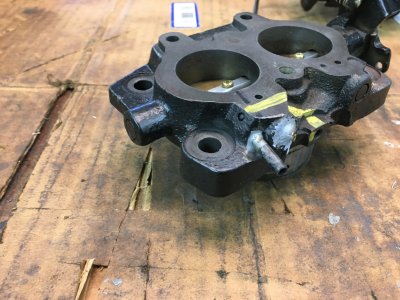
m
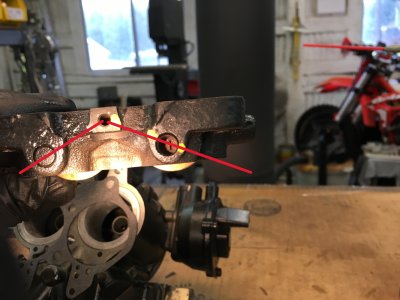
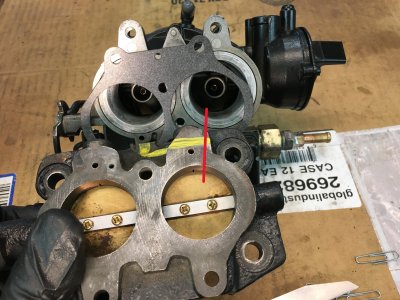
I cleared an area with a small burr and then used a spot facing bit to create a flat where I could measure carefully and mark where the hole was needed. This was the most stressful hole I think I’ve ever drilled.
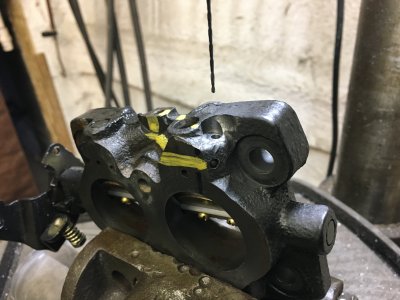
The hole came through the base just where I was hoping it would- just above the throttle blade. It felt a bit like operating a tunnel boring machine!
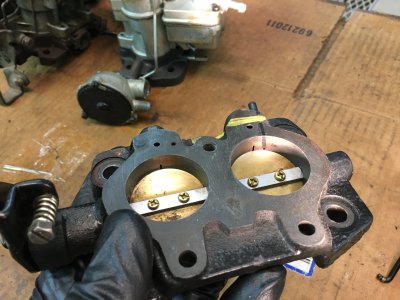
Placed a vacuum hose nipple into the outside of the hole with some epoxy; when that cures, I’ll reassemble and try it out. Fingers crossed!
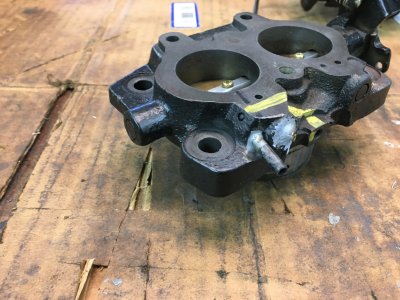
m